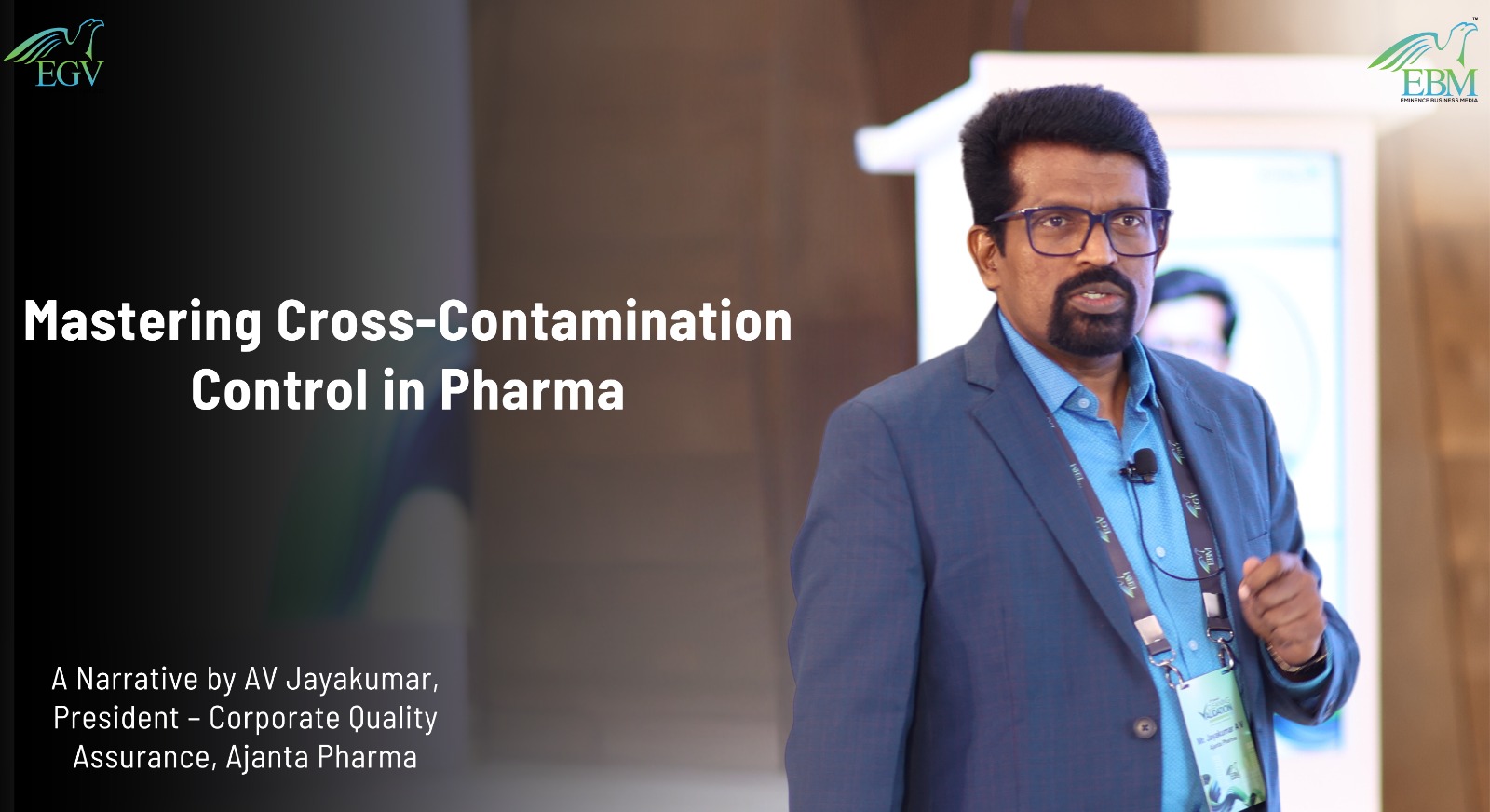
A Narrative by AV Jayakumar, President – Corporate Quality Assurance, Ajanta Pharma
In the high-stakes world where every action of Indian pharma companies is closely watched, cross-contamination is a challenge that requires constant vigilance. As someone deeply entrenched in the industry, AV Jayakumar has first-hand experience of how easily contamination can compromise a product’s integrity. During his recent conversation with the Eminence Team, he shared insights on why having a robust contamination control strategy is essential and how we can better protect our processes and, ultimately, our patients. Here’s what he has to say
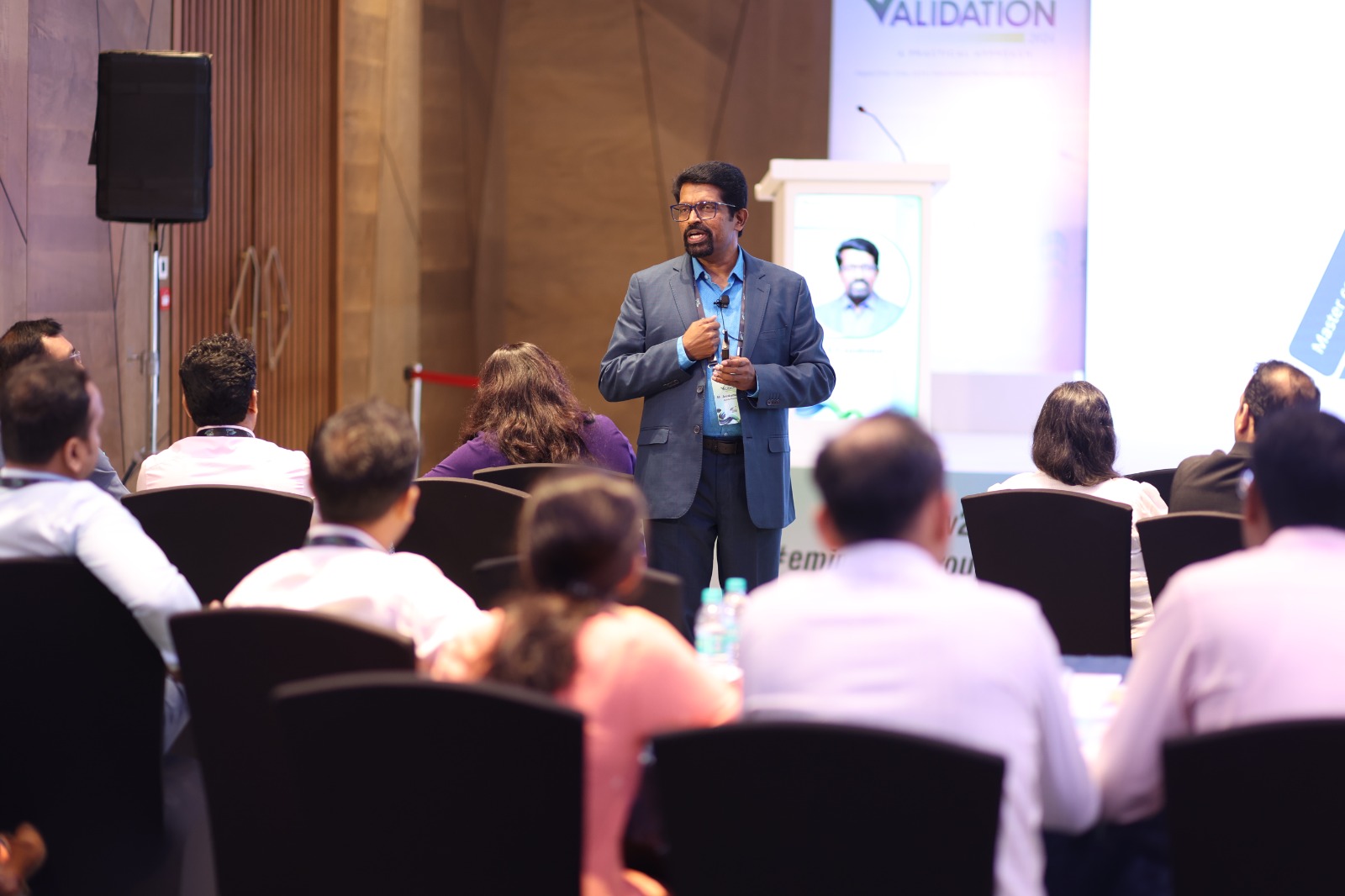
Understanding Contamination and Cross-Contamination
Before diving into solutions, it’s critical to understand the problem. Contamination is the unwanted introduction of impurities—chemical, microbiological, or foreign matter—into or onto a product at any stage of its lifecycle. Cross-contamination, however, is a different beast. It occurs when one product or material becomes contaminated with another during production, an exceptionally high risk in multiproduct facilities where the same equipment is used to manufacture different products.
I often ask colleagues, “Do you have a master contamination and cross-contamination strategy?” This isn’t just about ticking a regulatory box; it’s about building a foundation for quality and safety.
Critical Elements of a Contamination Control Strategy
A well-crafted contamination control strategy begins with the facility itself. The design, construction, and location of the manufacturing environment are foundational. The facility must be spacious enough for proper equipment placement, designed with smooth surfaces for easy cleaning, and structured to ensure adequate segregation of materials and products to prevent cross-contamination.
Environmental controls are another critical aspect. Proper temperature, ventilation, and lighting are not just about comfort but about maintaining product integrity. Zoning the facility based on air quality, for instance, can significantly reduce the risk of contamination. I’ve seen facilities where blending rooms are supposed to maintain positive pressure but instead operate under inconsistent conditions, leading to unnecessary risks.
Smooth, inert surfaces are non-negotiable when it comes to equipment. If a piece of equipment is difficult to clean, it might be wise to dedicate it to a single product. This reduces the risk of cross-contamination, particularly in a multiproduct facility.
Manufacturing Processes and Best Practices
Manufacturing in campaigns, where qualified cleaning processes and checks are performed between batches, is one of the best strategies to minimize contamination. Utilizing a closed manufacturing system, where the product isn’t exposed to the room environment, further protects against contamination.
Another critical practice is area line clearance. After each cleaning process and between batches, line clearance should be conducted according to approved procedures. This ensures that no remnants from previous batches remain, reducing cross-contamination risk.
Tackling Real-World Challenges
In my experience, real-world challenges often test the robustness of our strategies. For instance, I’ve encountered facilities where equipment washrooms are used to store cleaned equipment without proper validation of the decontamination process. This is a recipe for disaster. Proper cleaning validation must cover the entire equipment train, including product contact and non-contact parts.
One particular issue I’ve observed is the lack of specificity in cleaning protocols. For instance, swabbing locations should be clearly defined and justified, yet this step is often overlooked. Additionally, cleaning effectiveness must be periodically verified to ensure ongoing compliance.
Environmental factors, such as stagnant water or residue buildup, are also significant but often neglected sources of contamination. Routine cleaning and maintenance and immediate spill management are crucial to prevent microbial growth and maintain a clean environment.
Final Reflections
Cross-contamination isn’t just a regulatory concern—it’s a real threat to the safety and efficacy of our products. Reflecting on my experiences, it’s clear that a comprehensive contamination control strategy is essential. It’s not just about meeting regulatory requirements; it’s about ensuring that every product we produce is safe for the patients who depend on it.
Equipment surfaces are also a concern were dent and scratches are the major risk of contamination. Each change parts to be dismantled and to ensure their cleaning before connecting with the equipment. Seals also to be ensured for proper cleaning. During validation this is to be considered.
Sir,
Thanks you so much your details article for cross contamination and thought process and important for safety of product.
Sir,
Greetings of the day!!
Thank you very much dear sir for sharing!!
Cross contamination it’s very important topic for patient safety and product.