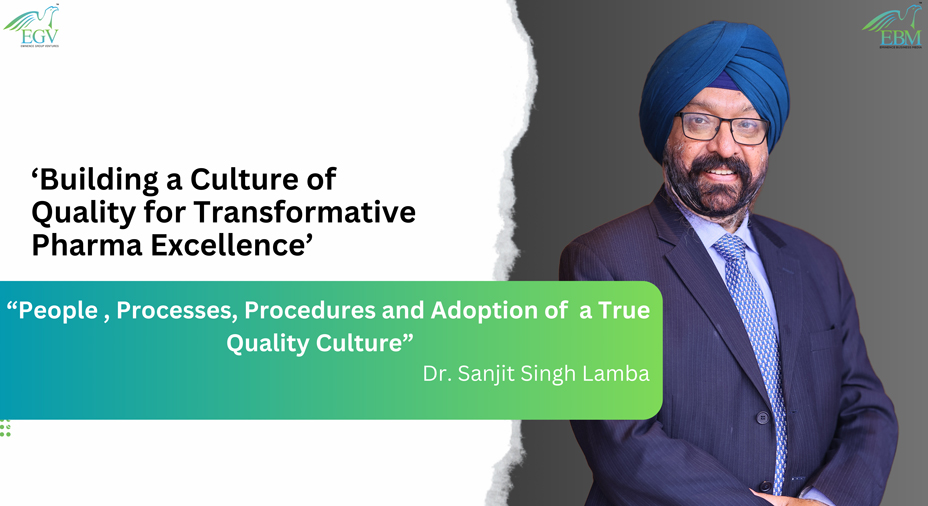
At its foundation, GMP (Good Manufacturing Practices) is a robust manufacturing framework engineered to uphold consistent product quality and integrity. Encompassing a breadth of critical elements – from meticulous hygiene and sanitation protocols to comprehensive quality management systems – GMP aims to mitigate and, ideally, eliminate substantial risks to quality like cross-contamination, mislabelling, and process failures.
Implementing Good Manufacturing Practices (GMP) delivers a host of benefits for life sciences companies. By minimizing waste, GMP enhances productivity and profitability while mitigating risks from recalls, compliance issues, and other problems. Ultimately, GMP serves as a protective shield, safeguarding both the company and its customers throughout the entire manufacturing process and ensuring top-quality products from start to finish.
In pharmaceutical manufacturing, the need for precise, repeatable processes is paramount. Ensuring the uniform production of drugs is essential for users to have confidence that their medicines contain the correct ingredients and quantities to achieve the intended effects. Manufacturers must have complete confidence that no deviations, adulteration, or contamination have occurred at any stage of the manufacturing process to ensure patient safety.
Quality cannot be retroactively “tested into” medicines. Instead, the only way to guarantee quality and consistency in drug manufacturing is through the meticulous application of standardized procedures by fully trained, motivated and accountable operating staff.
By focusing on the 5Ps (people, processes, products, premises, and performance) and implementing the necessary controls, manufacturers can be confident they are compliant and able to demonstrate their compliance to inspectors and certifying bodies as required apart from ensuring patient safety.
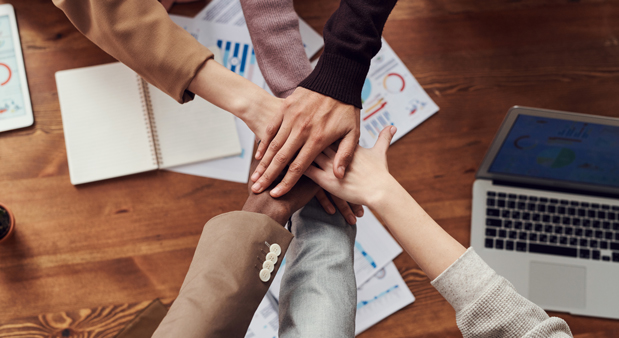
People
The company must establish clear roles and responsibilities for all personnel involved in drug manufacturing. Employees should receive comprehensive training on proper procedures and their performance should be regularly evaluated. Training methods should be periodically reviewed to ensure they remain effective in maintaining operator competency. A good quality culture is based on the behaviour of the individuals within the corporate quality strategy and the appropriate infrastructure of the company. It is important that everybody is aware of the importance of quality. Individuals need to transfer both knowledge and quality values. In an environment where the tolerance to quality issues is declining , people ,must adopt quality excellence as their core strength rather than just complying to requirements as tick box approach.
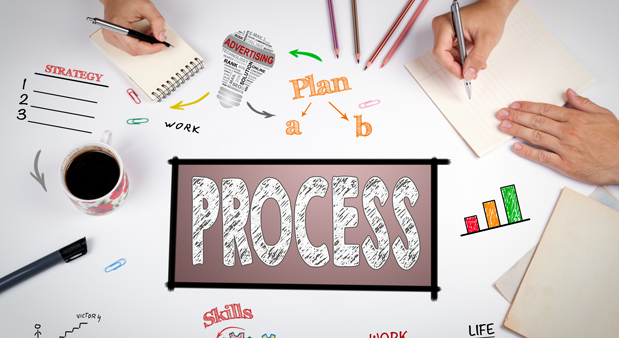
Processes
Processes are series of related tasks that transform inputs into outputs. Procedures are the prescribed methods for executing all or part of a process to ensure consistent results. Businesses must define and document their processes and procedures to provide clarity on what needs to be achieved and how to meet operational standards.
Established validated processes are essential for ensuring quality. They provide a consistent framework for operations, ensuring all activities adhere to defined standards. This minimizes variations and enables effective monitoring and improvement of quality across the organization, ultimately leading to reliable and high-quality products or services.
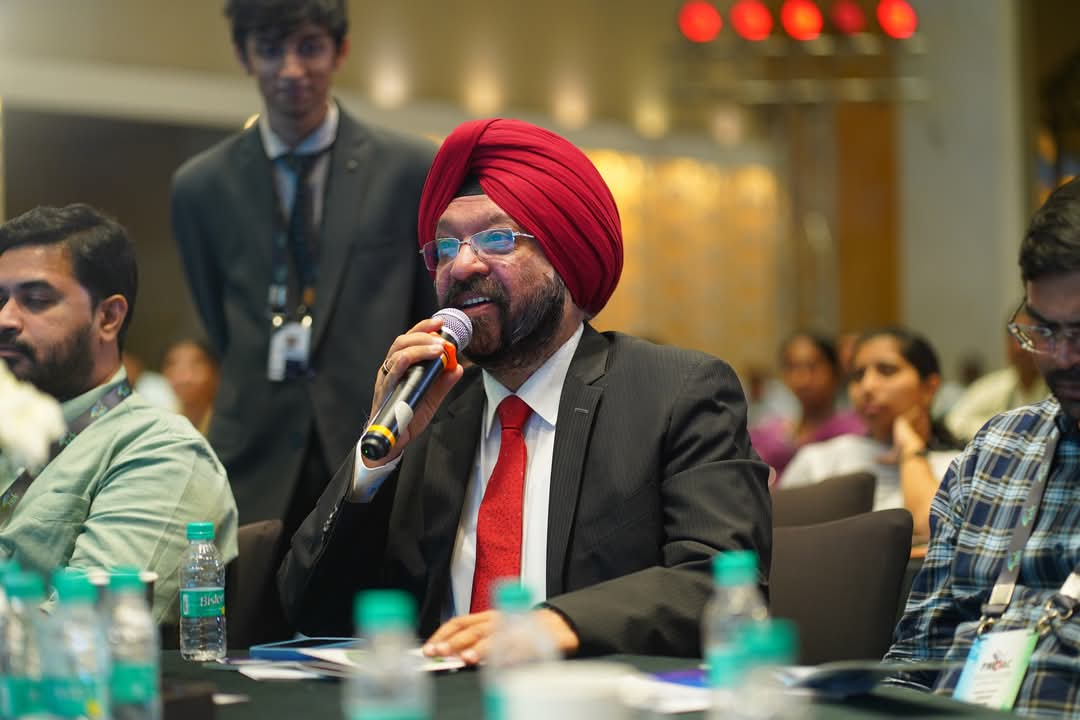
Procedures
All procedures must be clearly laid out and followed. Any deviations from standard procedure must be investigated and reported. Routinely recording data at key manufacturing stages enables faster identification of issues or non-conformances if a product batch needs to be recalled.
Established procedures are crucial for ensuring quality. They provide a standardized framework that promotes consistency across all aspects of a process. This leads to reliable and predictable outcomes, meeting customer expectations and minimizing errors. Additionally, these procedures facilitate continuous improvement efforts within the organization.
The ‘Ps’ (policies, procedures, and processes) are designed to ensure the quality and consistency of the end products for consumers. This end-to-end responsibility encompasses the proper handling and condition of all goods entering and leaving the facility.
For instance, manufacturers must have detailed specifications for all raw materials and components used in production. Additionally, they must have standardized methods for research, development, processing, manufacturing, packaging, testing, sampling, status control, stability testing, and record-keeping to maintain repeatability.
Quality in the pharmaceutical industry refers to the overall excellence and reliability of a product or service. A quality-focused approach takes a comprehensive view, encompassing all aspects of the drug manufacturing process – from sourcing raw materials through production and distribution.
Maintaining quality ensures that the drugs produced are safe, effective, and consistently meet patients’ needs. This involves rigorous testing and analysis to verify the drug’s identity, purity, potency, and stability, as well as adherence to standards and specifications.
The future of the pharmaceutical industry lies in embracing a proactive quality culture that prioritizes:
- A mindset of continuous improvement and shared accountability for quality outcomes
- A well-designed quality management system that balances consistent quality with compliance
- Reliable on-time product delivery
- Leveraging technology and automation to streamline processes and reduce errors
- Proactive monitoring of regulatory changes
This quality-driven approach folds compliance into a proactive system where regulations are the minimum requirements, not the ultimate goals. Quality control and assurance measures ensure each manufacturing step meets or exceeds standards. Real-time process metrics and controls act as an early warning system, allowing adjustments before products go out of specification.
The concept of quality culture has evolved over time in response to the growing need for comprehensive quality management systems. Traditionally, pharmaceutical companies relied on quality control, focusing on post-production testing. Over time, a paradigm shift has occurred, leading to the adoption of quality assurance principles and a proactive approach to quality management. This transition emphasized prevention rather than detection of defects. This development is now continuing with the establishment of Quality Culture concepts.
The pharmaceutical industry’s adoption of Quality Culture is transforming how organizations approach quality management. By emphasizing prevention, patient safety, and regulatory compliance, Quality Culture is becoming a cornerstone of successful pharmaceutical companies. While challenges exist in fostering a culture of quality, the benefits outweigh the obstacles.

Benefits of Quality Culture:
Improved Product Quality: A strong Quality Culture ensures all employees prioritize quality in their work. This commitment leads to higher-quality products, reducing risks of recalls, adverse events, and regulatory issues.
Enhanced Patient Safety: Quality Culture puts patient safety first. Robust quality systems minimize errors and ensure medicines are manufactured per GMP, safeguarding patient health.
Regulatory Compliance: Quality Culture aligns closely with GMP. A culture of quality facilitates GMP adherence, reducing compliance risks and enhancing regulatory relationships.
Increased Efficiency and Cost Savings: Integrating quality into all processes allows early issue identification and resolution. This promotes efficiency, reduces waste, and delivers long-term cost savings.
A true culture of quality is an environment in which employees not only follow quality guidelines but also consistently see others taking quality focused actions and hear others talking about quality and feel quality all around them. As a quality focused organization leaders must find a new approach to quality, one that moves beyond the traditional total quality management tools of the past to a Culture of quality excellence, in which employees live quality in all their actions where they are passionate about quality as a personal value rather than simply obeying an order from the top.
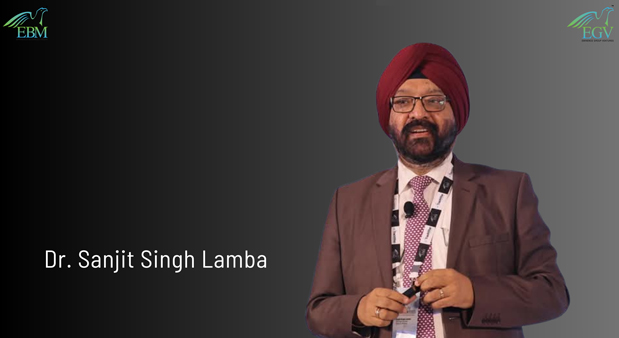
Amazing
Excellent message
Much more informative to create Good quality culture throughout the organization resulting quality products followed by Quality by Design. (QBD) Thanks a lot.
With best regards,
Arvind Dixit
Head-Quality
95415 28840