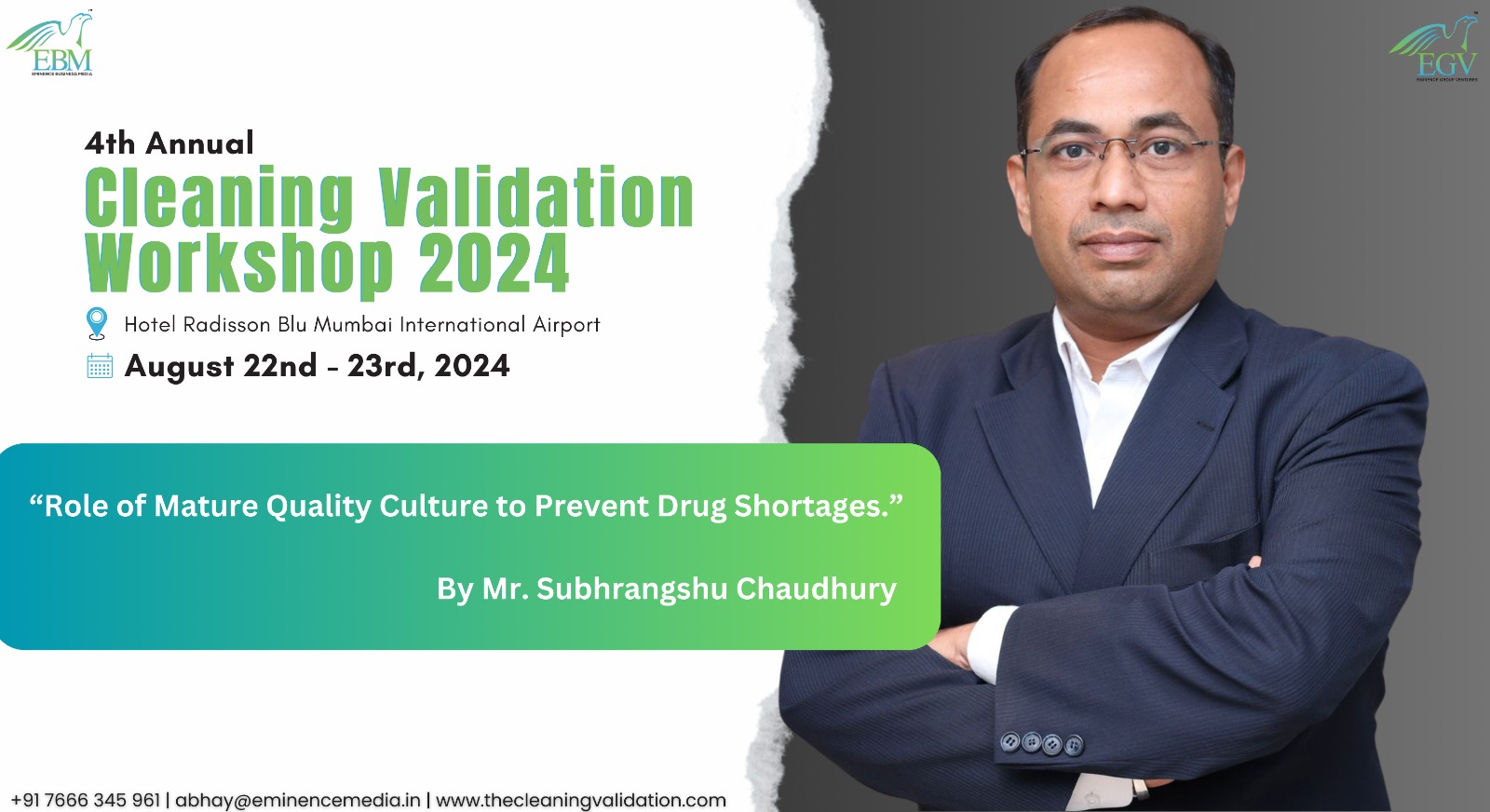
Subhrangshu Chaudhury
Vice President & Head of Quality
Centaur Pharmaceuticals
Over the past few years, the term “Quality Culture” has become quite a buzzword. I recently attended a conference where senior leaders across different industries were discussing this topic. It triggered my thoughts. I am a quality leader who has worked in pharma for almost two decades and came from the shop floor. Let us first try to understand why quality culture plays a significant role now in almost every industry specifically in my field, the pharma industry.
As a pharma professional, our role is to provide; Safe, Effective, and Quality medicine to the patient without any disruption as neither the patient nor their doctor desires to change the medicine or the brand frequently.
A study of 650 physicians in the US found that 79% of physicians had patients who experienced difficulty obtaining medicine due to drug shortages. In the case of cardiologists, dermatologists, and rheumatologists, the percentage was over 85%. As per the report published by USFDA 62% of the drug shortages in the calendar year 2013 to 2017 were mainly due to Quality issues. The percentage was reduced to 40% in 2022 – 2023.
The supply disruptions were mainly due to two reasons:
1) Bad inspectional outcome and
2) Market recalls due to quality concerns.
Inspection Management:
I have frequently encountered a question; people are curious to know how to prepare for an inspection or what should be done to keep the facility “All time ready” for an inspection. My answer to that is, you cannot really prepare for an inspection. If you are open for business every day, you should be ready for inspection every day.
“You cannot prepare for an inspection. If you are open for business every day, you should be ready for inspection every day.”
The logic behind my putting is if you notice the observation trend of “Form 483” issued by USFDA after every inspection from 2015 it all started with “Data Integrity” then in 2018 “inadequate investigation” and now it is continuing with “Cleaning” and “Cross-contamination”.
Now do you think that for all these points preparation is a prerequisite? The answer is you cannot prepare anyone “to stop or not to stop on the red light on a traffic signal whether police or camera is there or not”. Similarly, you cannot prepare that we need to do contemporaneous entry what we do or we need to do what is written in the SOP. It should be in our culture. The previous residue should be cleaned before starting fresh next product and taking cleanliness seriously in the pharma industry should be an integral part of the culture. We cannot be prepared before the inspection.
Hence, the winding up point is if we take care of our culture then compliance will be automatically taken care of. Our focus needs to be changed from compliance-centric to patient-centric. We are dealing with Drugs and if a small dosage of the drug can cure then a small impurity present in the same drug can be life-threatening to the patient. Audit or inspection is a bare minimum regulatory requirement which is nothing but a license to sell our medicine.
So, we cannot contemplate that a 5-day or 10-day inspection will determine the quality of the medicine. We need to remember that the family members could consume the medicine. We are dealing with sick people, sometimes with the people who are on the roller coaster ride of life and death; they are taking our medicine with high hopes that they will be cured after taking our medicine. So, in simple words, we are dealing with a field where we bring a ray of hope in the darkest phase of a patient’s life.
In other industries, if the quality of a car or a mobile is substandard then we can replace the same with another car or mobile but in pharma, we cannot replace a life with another life.
Supply disruptions:
Supply disruption can happen due to recalls like the Nitrosamine saga we all are aware of or some products that are developed in a hurry to meet the deadline to achieve the market may fail in commercial production. So here also it relates to the culture of the organization.
Other frequent causes of supply disruption may be found in day-to-day events such as
- Out of Specifications
- Deviations
- Machine breakdowns
In such a scenario, we need to understand that to reduce these disruptions we need to improve our quality culture; like when we are investigating an OOS; what is our culture to close the investigation? Is our culture to somehow invalidate the OOS and release the batch or to identify that exact root cause find the true quality of the batch and take a CAPA so that similar OOS should not happen again?
Similarly, when we are closing a deviation, our culture is to just close the deviation at the month’s end and release the batch with ‘Training’ as a CAPA or are we trying to identify the exact root cause so that in future this deviation should not come and disrupt our day-to-day activity or more over similar market complaint should not come.
What is our culture to perform preventive maintenance? Are we doing predictive maintenance instead of preventive maintenance?
Before having an out of specification there will be some out of trend so are we taking proactive measures to prevent the out of specifications during out of trend investigation? Similarly, before going for a machine breakdown, machines will give some alarms. So as a company culture are we trending those alarms or trying to predict when the breakdown may happen and taking a proactive preventive maintenance which is called predictive maintenance?
So it all encapsulates “Quality culture” but who holds the baton of quality culture – management or shop floor?
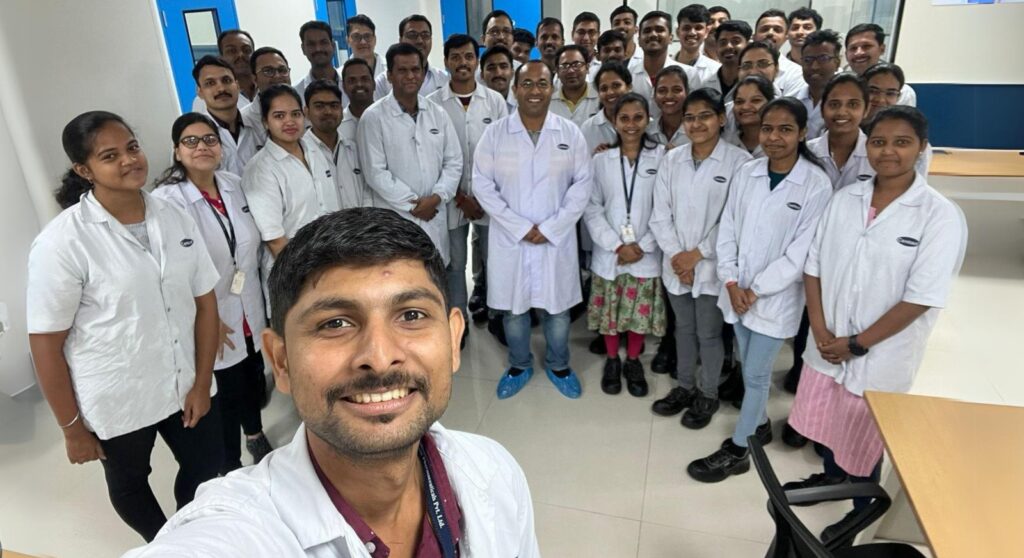
Culture always starts from the TOP. Leadership plays a crucial role in setting the tone of the organizational culture. So, when we are canvassing about the strategies to promote transparency in the organization, incipiently we have to think about whether the senior leadership in the organization is ready to hear bad news. Because down the line at the operator level or analyst level, people will only divulge those things that are preferred by their higher authority and leaders. To promote transparency, we need to promote the “speak up” or “VoE” (voice of employee) culture in the organization. Operators and analysts are the only people who know the real picture of the shop floor so if we pay attention to their words and encourage them to share the real picture then definitely, we can incorporate a lot of precautionary measures in our system proactively.
To promote accountability, we need to promote empowerment. If we only promote “speak up” or “VoE” culture without empowerment then we all will get to hear the same line “yeh toh sab ko pata hai” (Everyone knows it). “Sab ko pata hai” (everyone knows) is ok but the onus lies with whom to correct the same. If we take the example of the automobile industry in Japan, we can easily find out, that they empowered an operator also to pause the production line if any inaccurate incident happened and rectify it. Similarly, we also need to empower our lowest down-the-line person to take the necessary action in case of any inaccurate incident.
Finally, in the Quality Management Maturity white paper published by USFDA, it is eloquently written that “Quality culture is an environment in which those who have responsibility for oversight and control over manufacturing take ownership for quality. Empowered employees will be always engaged and engaged employees understand and care about how their roles within the organization impact patients and consumers, product quality, and product availability. Engaged employees at all levels take ownership and are empowered to identify, communicate, escalate, and initiate changes that continuously improve processes, procedures, and practices”.
—————————————————————
Quality in culture is only way for ATR ( All Time Ready)..well written sir…
Spot on! Always a delight to read your writings! A must read for all working in Pharma! We need to follow this culture & mind set.
Well articulated message
Very true. It is the responsibility of each and every employee to ensure issue are identified, and escalated and resolved on time.
Quality culture can happen only only in a designed way of working, where the top management , middle management and the shop floor are connected with one aim one Goal and one team. Again I am saying with a frame work only, it is possible.
Nicely articulated and connected the Dots.
Nice articulate sir about drugs shortage to Quality culture.
Quality Cultural is mostly depends on the culture of Do it right in first time.
Quality Cultural ∝ to QMS cultural of that organization.